Design and Simulation of an Electric Tuk-Tuk
Conventional, diesel/petrol driven Tuk-Tuks are not used as a medium of transport in most countries in the world. However, they have emerged as a great option in bustling, busy cities where traffic and mobility are huge inconveniences. They are common in countries with tropical climates and in developing nations since they are relatively inexpensive to use.
Being from Thailand, I have grown up travelling in Tuk-Tuks, and so I decided to model and simulate it. Recently, I’ve also come to realize that the electrification of Tuk-Tuks is easier than that of cars or buses. Through a battery disposal-and-replacement method, it could be possible to hybridize E-tuktuks with an effective Battery-Ultracapacitor combination. This could make Tuk-Tuks a more viable option in many more developing countries and thus accelerate the process of electrification to make a positive impact to climate change. That is also what I want to evolve this project to eventually, since currently I’ve built this using a battery only.
Expanded overview of the model:
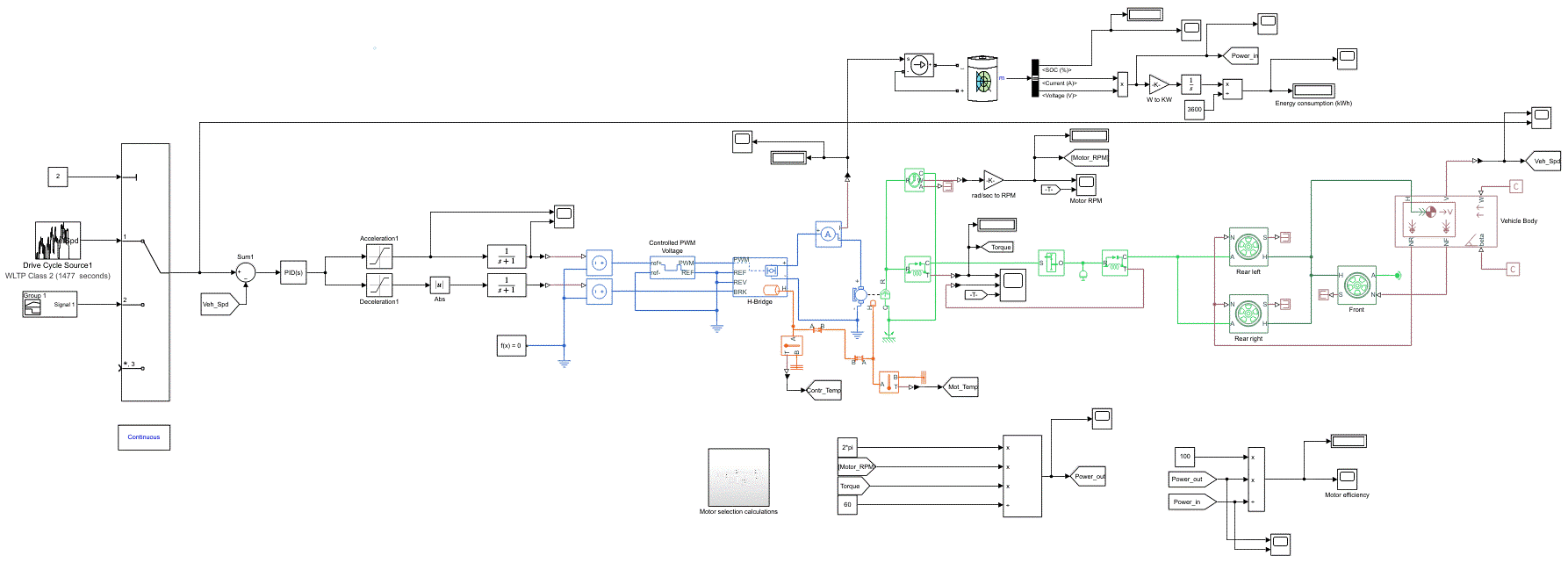
Condensed into subsystems:
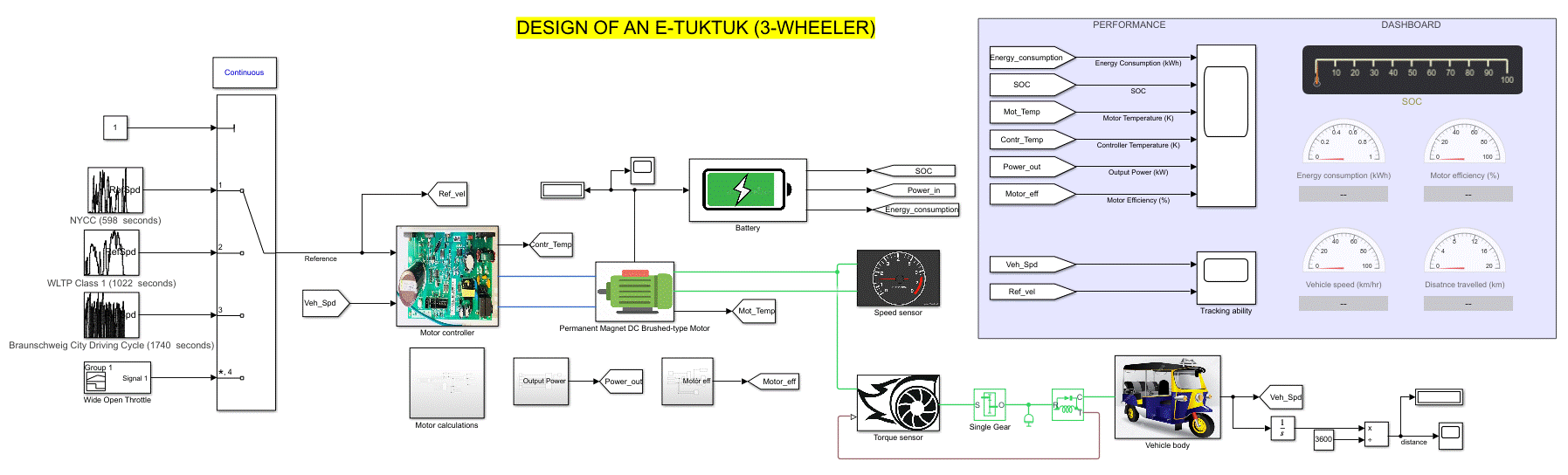
Simulating motor control and PMDC motor:
PWM voltage generator and bi-directional power converter make up the motor controller
The H-bridge power converter receives supply from a PWM generator, controls the power according to the vehicle requirements and transmits it to the motor.
If the accelerator signal is given, the PWM block converts that signal into the appropriate voltage needed to supply to the motor. When the brake signal is given, this bi-directional power converter takes in current from the vehicle and transfers it to the battery to charge it.
Results of the simulation:
Drive cycle #1 - NYCC (598 seconds)
Even with custom PI/PID tuning, the vehicle is unable to track this drive cycle with good accuracy. It is quite messy, as evident. This seems to be a very difficult reference cycle to follow because of the number of times the vehicle needs to accelerate and brake. The time period between those commands is also very short, making it highly difficult to follow precisely.
Negative energy consumption means more energy is flowing back from the motor (which acts like a generator too) to charge the battery than is leaving the battery. Obviously not all of the energy recovered during regenerative braking can be used to charge the battery. Charge voltage/current also differs from discharge voltage/current, which is why the SOC isn't at 100% despite more energy coming in than going out.
SOC and Energy Consumption graphs are not at their optimal values here, since the vehicle was unsuccessful in accurately tracking the drive cycle, and hence consuming more energy to try to meet the demand. If the vehicle tracked the reference well, energy consumption would be even more negative and SOC would be closer to 100%.
Motor efficiency seems to fall mostly between 40-80%.
Drive cycle #2 - WLTP Class 1 (1022 seconds)
Vehicle tracks reference with good accuracy. Due to this, performance parameters such as energy consumption and SOC are close to their optimal values.
Effects of regenerative braking are clearly seen in SOC and Energy Consumption graphs as the battery keeps getting charged.
Apart from the two spikes, motor efficiency mostly falls between 50-95%. This number could be a lot more precise and more importantly consistent at a high value (80%+) if current had fewer fluctuations.
Drive cycle #3 - Braunschweig City (1740 seconds)
Vehicle tracks reference fairly accurately.
Motor and controller temperature are still under control despite this being the largest drive cycle, but controller temperature hit a peak of 323K, which indicates that a better thermal management technique needs to be in place.
Motor efficiency is mostly falling in between 50-80%, barring that one spike at 1300sec.