Design and Thermal Modelling of a 10S1P Battery Pack
High capacity rechargeable batteries are what make electric vehicles a practical reality. At the same time, several limitations in the EV arena today exist due to batteries too — charging time, range concerns, and thermal management for instance. Battery technology and chemistry are at the forefront of innovation and attention, and even minor improvements will significantly accelerate the transition to a sustainable future.
However, it’s not just about how much energy a battery pack can store, improving their capacity and how long they last. It’s more about how that stored energy can be maximized during each cycle. Lithium-ion batteries are sensitive, and how they hold up under different conditions will determine key vehicle performance parameters such as range and durability of both the vehicle and the battery pack.
This project includes testing a pack of 10 Lithium-ion NCR18650PF cells connected in series under normal and extreme conditions, to understand how their performance differs, and how they must be maintained so that their best can be extracted.
Overview of the model:
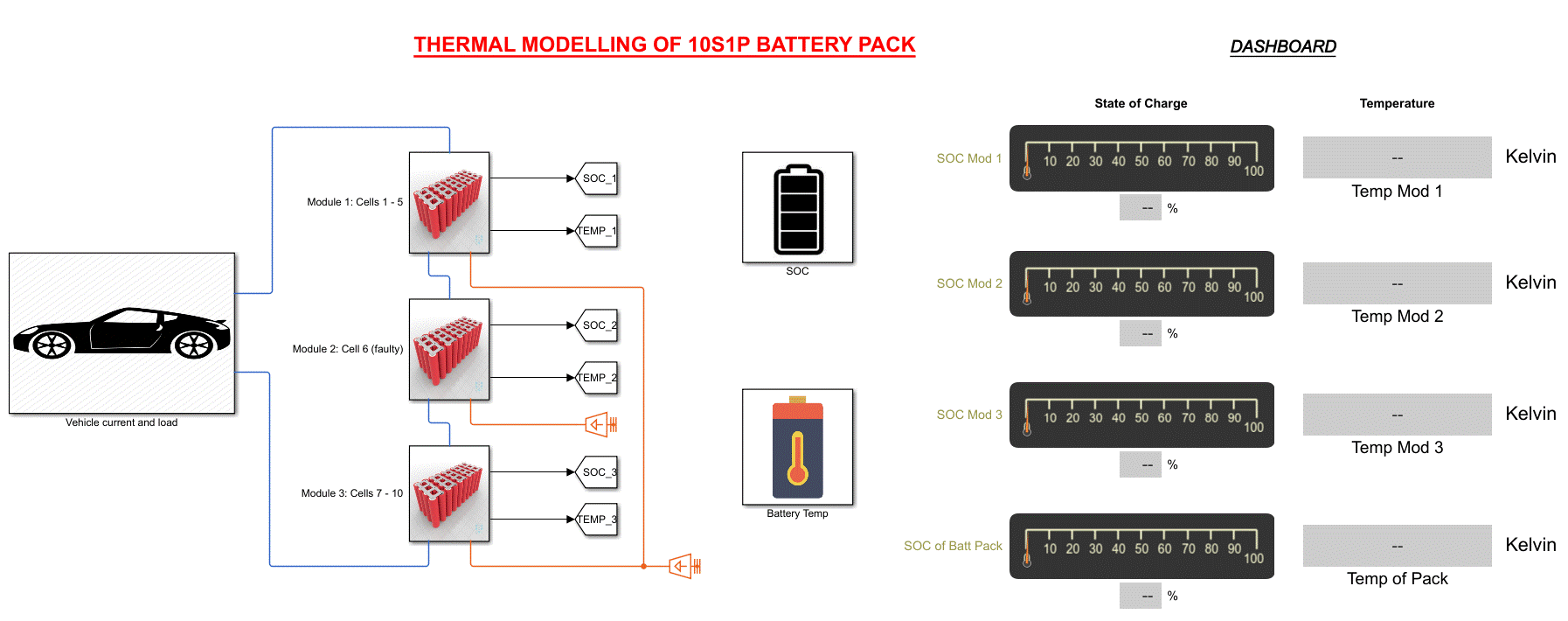
Three modules have been connected together in series to make a 10 cell battery model.
A fault has been introduced in Cell 6 by adding some ohmic resistance. This has been done to demonstrate the effect of the faulty cell on the entire pack.
UDDS cycle (current vs time) has been used to charge/discharge the batteries for 1 hour.
All cells are initially at 25 degree C.
A temperature source is used to test the cell performance at four ambient temperatures: -10 degree C, 0 degree C, 25 degree C, 45 degree C.
Convective and conductive blocks have been added for heat transfer between blocks.
Working of the model:
Battery modules:
-
Module 1: Cells 1 - 5
-
Module 2: Cell 6 (faulty) - an external resistor of 5 Ohms is added
-
Module 3: Cells 7 - 10
Results of the simulation:
Exposing battery modules to hot temperature (318K or 45C):
Heat will flow into batteries from source
Exposing battery modules to cold temperature (273K or 0C):
Heat will flow away from batteries towards source
Further development:
10S8P battery pack 3D model designed using Solidworks
One way to advance a model-based design project is by constructing a CAD geometry of the model, and then combining it with a dynamic simulation to understand how they work together.
Performing a co-simulation by integrating the MATLAB/SIMULINK simulation shown in this project with the 3D Solidworks model on the left through Simscape Multibody is how I aspire to take this thermal modelling battery project further.
That would enable an in-depth exploration of how feasible the design is for real-world application and also help visualize more problems and solutions.