Design and Simulation of a Tesla Model 3 (PMDC motor)
This project presents a MATLAB/SIMULINK model of the Tesla Model 3 (TM3) battery electric vehicle (BEV) powered by a PMDC motor. TM3 actually uses an (I)PMSM motor, however, this was one of my earliest projects and I was unfamiliar then with the sophistication needed to model a PMSM motor. I later went on to model the TM3 with a PMSM motor nevertheless, feel free to check it out here!
How a BEV with a PMDC motor is typically modelled:
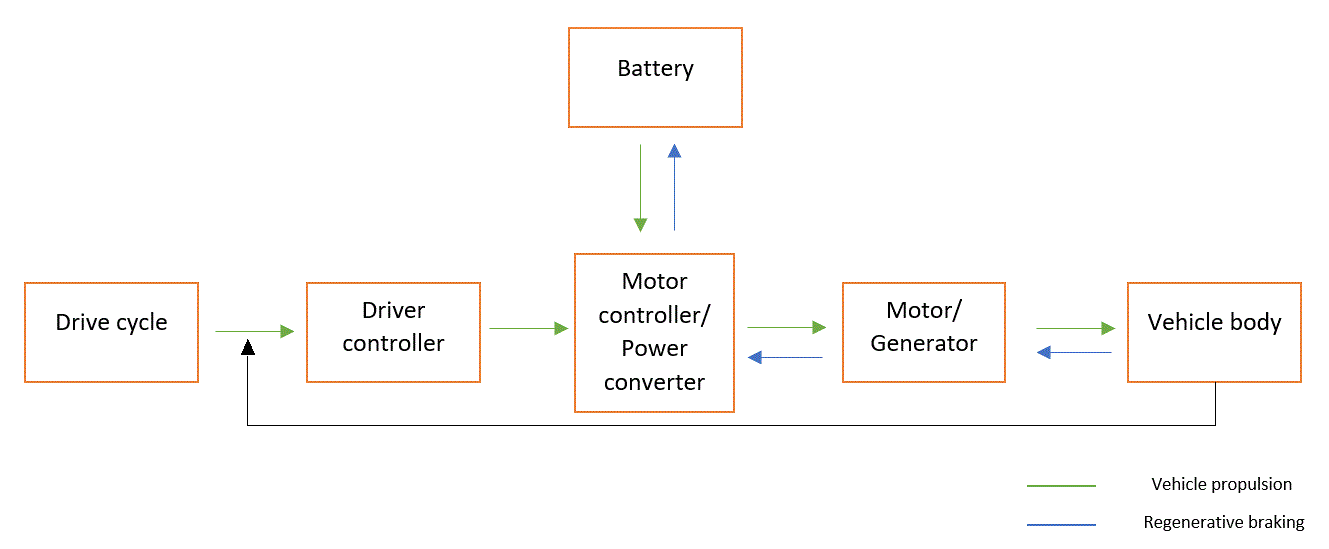
Short summary of how this model works:
A reference drive cycle is given to a driver, which is basically a PID controller that tries to minimize the difference between the actual vehicle velocity and the reference velocity by generating acceleration and brake commands. The battery provides electrical power to the motor, which converts it to mechanical power and powers the motor. However, if the battery is directly connected to the motor, the vehicle would be running at constant speed as there would be no control. A motor controller is a power converter that bridges this gap and controls the speed and voltage provided to the motor, which then powers the wheels and propel the vehicle.
Overview of the model:
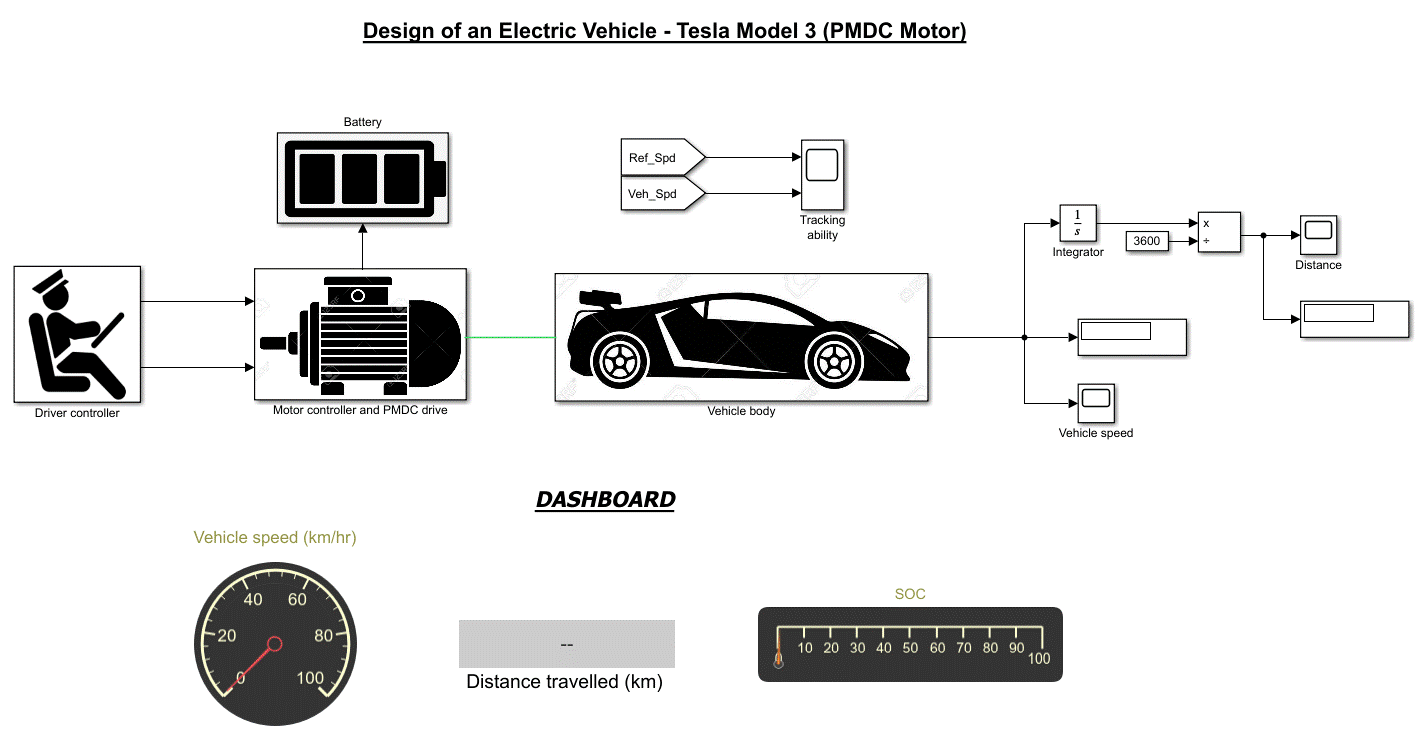
Working of the model:
Simulating motor control and PMDC motor:
PWM voltage generator and bi-directional power converter make up the motor controller
The H-bridge power converter receives supply from a PWM generator, controls the power according to the vehicle requirements and transmits it to the motor.
If the accelerator signal is given, the PWM block converts that signal into the appropriate voltage needed to supply to the motor. When the brake signal is given, this bi-directional power converter takes in current from the vehicle and transfers it to the battery to charge it.
Results of the simulation:
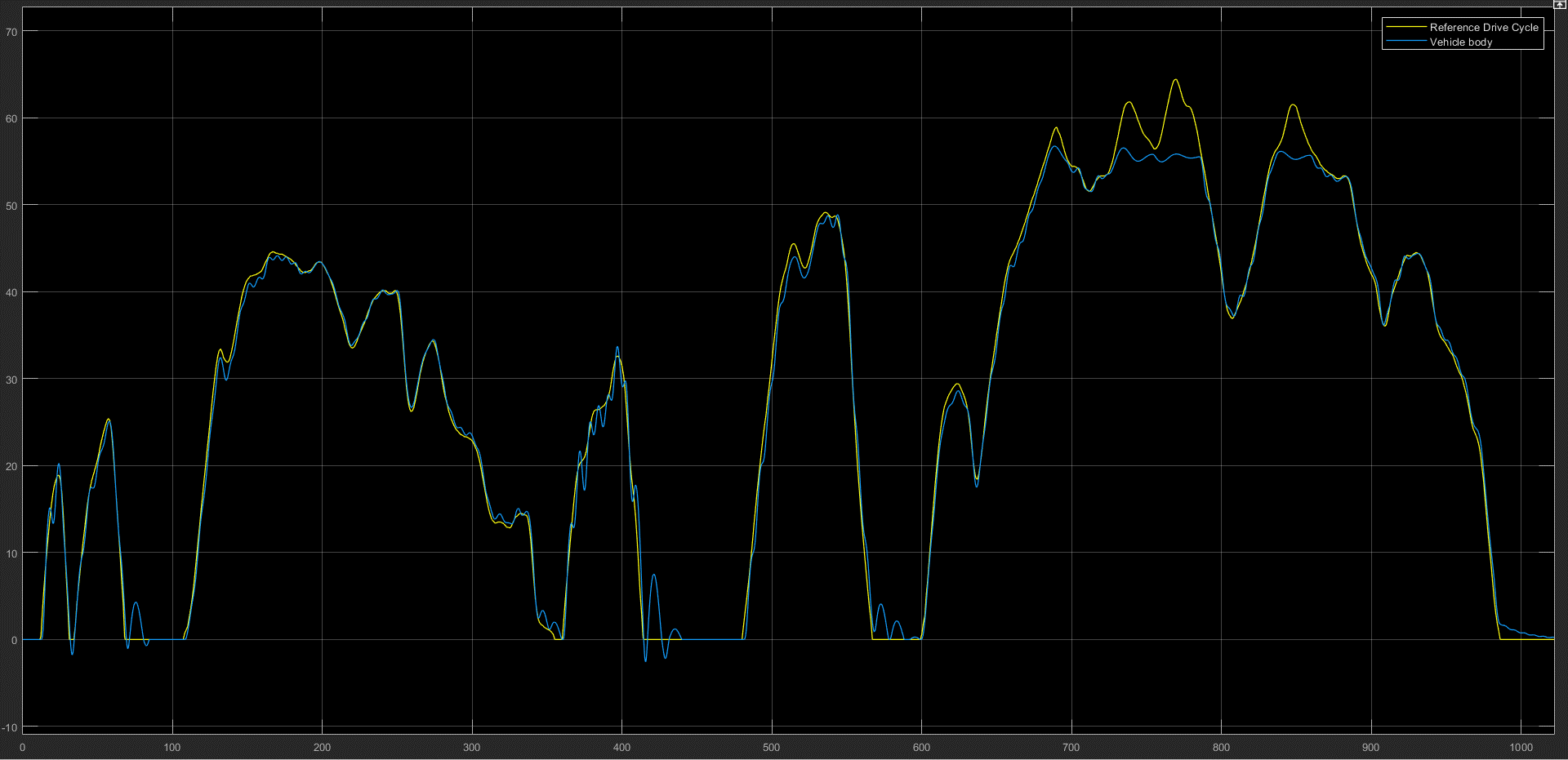
The vehicle has been able to meet the drive cycle fairly, barring the 50 seconds between 700-800s. This is due to the insufficient no-load speed of the PMDC motor chosen. A slightly higher no-load speed or a PMSM motor would be sufficient to meet the current drive cycle requirements.

The SOC of the battery has only reduced from 100% to 98.5%. The main reason is that the Tesla Model 3's rated battery capacity is about 139Ah, which is considered high. Higher ampere-hours rating results in more power and more performance. Moreover, the WLTP drive cycle was only 17 minutes long with a lot of deceleration curves, as seen by the negative currents, which consistently allowed the battery to recharge through regenerative braking.